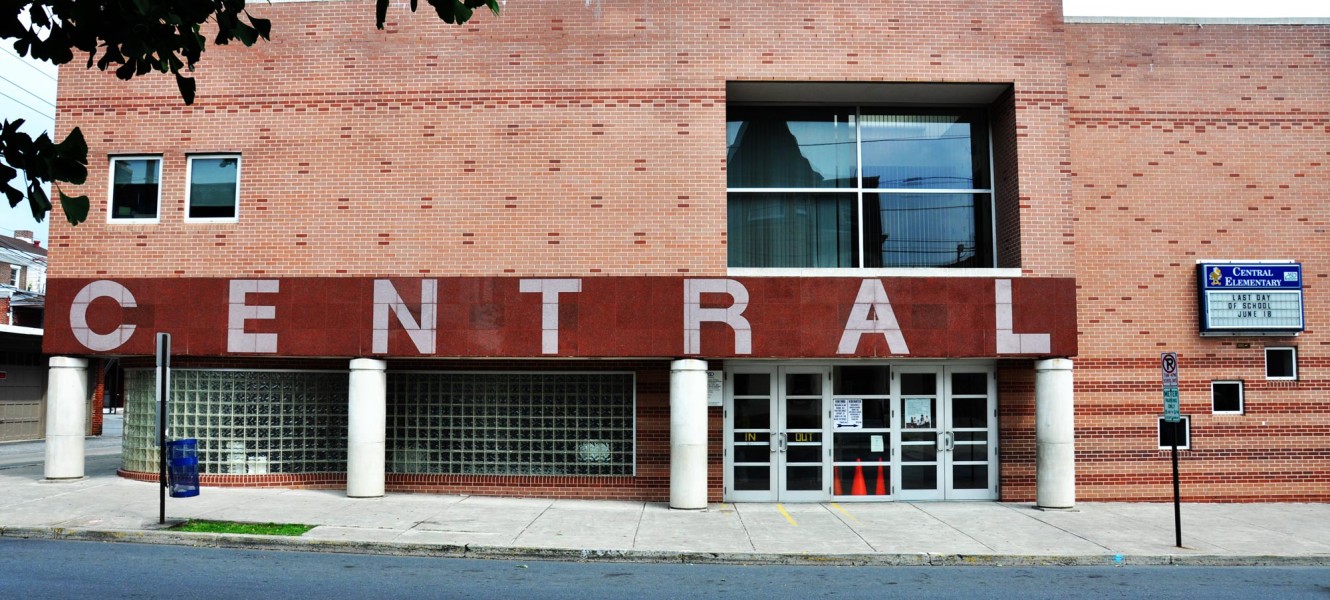
Allentown Boiler Replacement Project
Allentown School District
Natural gas is becoming a popular choice for many school districts due to some of the advantages it has over heating oil. The biggest advantage is cost; natural gas is typically a much cheaper fuel option than fuel oil. Not only is the cost of fuel oil more expensive, but the maintenance and liability costs are also higher for fuel oil than natural gas. The use of fuel oil as a heating source requires the use of large underground storage tanks (USTs) and each tank is often insured, which can cost as much as $1500 per year. The insurance cost can add up quickly for a school district that may operate many USTs throughout the District. Routine maintenance of USTs is extremely important, but it does not eliminate all risk. Tiny holes can be missed during inspections, and even a small hole can cause significant contamination. This makes fuel oil tanks a significant environmental risk. This has motivated many school districts to remove their tanks and replace their boiler room systems with natural gas heating.
The initial cost for a boiler replacement project may be high, but through the Pennsylvania Guaranteed Energy Savings Act, the cost will be fully reimbursed in energy savings each year over a 15 year period. If the energy savings are not realized during the allotted time period, the qualified Energy Services Company (ESCO) who procured the contract will be held accountable for the proposed savings.
The Allentown School District weighted their options with the help of Johnson Controls experts decided it was time that they start saving money at Central Elementary School. The boiler was fueled by a 10,000-gallon No. 2 fuel oil steel underground storage tank that was installed in the 1960s. It was the oldest of all the district’s tanks. The boiler and piping potentially contained asbestos insulation, which required testing and abatement before the project could move forward. This project is an example of how Element Environmental Solutions (E2S) can provide environmental consulting on a project from the inside out. The IAQ team conducted an asbestos survey and prepared abatement specifications while the site assessment team managed the tank removal specifications, oversight, and environmental site assessment activities.
Central Elementary is located in the heart of downtown Allentown and does not accommodate heavy machinery well. Coordination challenges presented themselves on the first day of the scheduled tank pull due to the multiple construction projects that were occurring in conjunction with the boiler system replacement. Communication was key to coordinating construction activities without interfering with the school’s ongoing projects. The UST removal was completed, following the guidelines established by the Pennsylvania Department of Environmental Protection, within the time constraints agreed upon in the contract documents.
Field screening activities indicated that a leak may have been present prior to tank removal activities, but the lab results indicated that the release was isolated and limited to the supply and return lines.
A portion of a former building foundation was located next to the tank. It is common to find that new development has occurred on top of former building foundations or to demolish a building and leave much of the construction debris in place as fill material. This tank was likely set in an old basement area and backfilled using limestone screenings and other urban fill. There was no soil in this area when the tanks were installed in the 1960s. Odors and VOC readings near the supply and return lines going into the building were relatively high. Field screening with the assistance of a photoionization detector (PID) indicated that the VOC readings and odors dissipated with depth. By the time native soils were encountered, approximately 12’ below the piping, the VOC readings were less than 1 parts per million. The steel tank was found to be in very good condition when it was removed from the excavation. Other than naphthalene detected at very low levels in one sample, no fuel oil parameters were detected beneath the lines or tank. E2S prepared a tank closure summary report detailing the tank removal activities and closed out the project in a timely fashion.
E2S’s IAQ team continued to manage the asbestos abatement project in conjunction with the tank removal. The boiler system’s hot water tank insulation and rib gasket insulation were comprised of friable asbestos containing material (ACM) that required safe handling during demolition of the boiler system. Element provided contractor oversight and indoor air quality monitoring during abatement and post removal. E2S conducted daily air samples inside and outside of the boiler room during the removal of asbestos found in the boiler room to ensure the contractors were safe and that no fibers were leaving the work space. Clearance testing was performed to clear the room for occupancy to allow demolition contractors to dissemble the boiler and its associated piping. Background samples were collected after the boiler was dissembled that failed the Environmental Protection Agencies (EPA) asbestos abatement re-occupancy criteria. The abatement contractors were called back in to re-clean the work area and boiler room. Immediately following the cleaning, E2S conducted another round of clearance samples and found that the area was safe re-occupancy.
This project was a great opportunity for E2S to demonstrate a few of our indoor and outdoor environmental services as well as effectively coordinate several projects occurring simultaneously.